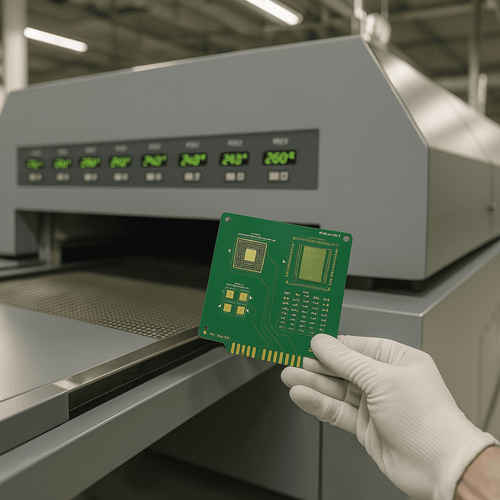
Understanding Reflow Profiles
A reflow process typically consists of 4 distinct stages: preheat, soak, reflow, and cooling. Each stage is carefully controlled to ensure your solder paste wets and solidifies as intended. Understanding how the stages affect your process and optimizing your operation for your material sets is key to achieving high reliability in your process.
How Reflow Profiles Affect Component Reliability
Here’s a quick overview of the different reflow stages and how they can impact component reliability:
- Preheat Stage: The preheat stage gradually raises the temperature of the PCB assembly to prevent thermal shock to the components. A rapid temperature increase can cause components to crack or delaminate.
- Soak Stage: During the soak stage, the temperature is held steady to activate the flux in the solder paste and remove any oxidation. If the soak time or temperature is not correctly managed, it can lead to insufficient flux activation, resulting in poor wetting and weak solder joints.
- Reflow Stage: The reflow stage is where the solder paste reaches its melting point and forms a bond between the components and the PCB. If the peak temperature is too high, it can cause component warping or damage to sensitive materials. Conversely, if the temperature is too low, the solder may not fully melt, leading to incomplete or weak joints.
- Cooling Stage: The cooling stage solidifies the solder joints. Rapid cooling can introduce thermal stress, causing cracks or voids in the solder, while slow cooling can result in large grain structures that are more prone to failure under thermal cycling.
Reliability Issues from Improper Reflow Profiles
Improperly designed or executed reflow profiles can lead to long-term reliability problems, especially where flux activators are concerned.
- Un-Reflowed Flux: Components exposed to improper reflow conditions may have a reduced operational lifespan due to inactivated flux residue remaining on the board. The activators left over can be a major source of ionic contamination and can greatly reduce your component life.
Optimizing Reflow Profiles with Magnalytix
At Magnalytix, we understand the critical role that reflow profiles play in component reliability. With our extensive experience in electronic reliability, we can help you develop and optimize reflow profiles that ensure strong, reliable solder joints and protect your components from thermal damage. Here’s how we can help:
- Profile Development: We work closely with you to provide objective evidence that reflow profile is optimized for electrochemical reliability and provide suggestions to ensure your reflow process is conducive to a clean assembly.
- Advanced Testing Methods: To provide this objective evidence, we utilize Surface Insulation Resistance (SIR) testing to identify the harmful effects of the flux residue, and Ion Chromatography (IC) testing to quantify the left-over ionic contaminants from your assembly process.
- Comprehensive Analysis and Recommendations: Beyond just providing data, our team offers in-depth analysis and actionable recommendations based on our decades of experience. We help you understand the root causes of any issues and implement solutions that enhance the reliability of your products.
Conclusion
The reflow profile is a critical factor in ensuring the reliability and longevity of your electronic components. By carefully managing each stage of the reflow process, you can prevent common issues and produce more reliable products. At Magnalytix, we are dedicated to helping you optimize your manufacturing processes. Our advanced testing methods and expert consultation services are designed to provide you with the insights and solutions you need to achieve the highest levels of quality and reliability.
For more information on how Magnalytix can help you optimize your reflow profiles and improve component reliability, contact us. Together, we can build electronic assemblies that stand the test of time.