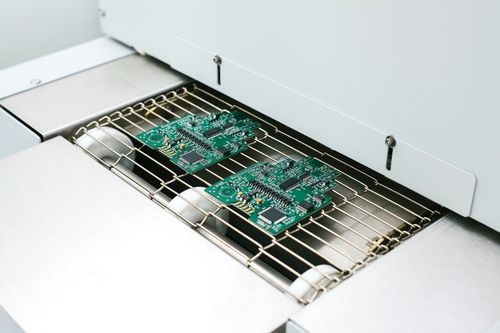
Understanding the Role of PCB Cleaning
Printed circuit boards (PCBs) are at the heart of every electronic device, but during manufacturing, they accumulate contaminants—flux residues, oils, dust, and more. These residues may seem insignificant, but they pose serious reliability risks, especially in high-reliability applications. Cleaning is not just a cosmetic step; it’s essential to eliminate these residues and ensure long-term performance.
To achieve reliable and consistent cleaning results, manufacturers must focus on three critical areas: Cleaning Agent Selection, Cleaning Machine Selection, and Proper Rinsing. Each one plays a pivotal role in removing harmful residues and ensuring your assembly will perform as designed—today and over time.
How PCB Cleaning Impacts Reliability
Cleaning Agent Selection
The right cleaning agent is the foundation of an effective cleaning process. Not all fluxes, solder pastes, or contaminants are the same—and neither are cleaning solutions. Water-based cleaners, solvent-based options, and semi-aqueous solutions each have distinct strengths depending on the materials involved.
- Impact on Reliability: Choosing an incompatible cleaning agent can leave behind harmful residues, fail to remove ionic contaminants, or even damage delicate components.
- Best Practice: Match the cleaning chemistry to your process materials and contamination profile. Ensure compatibility with your board finishes, components, and residue types.
Cleaning Machine
Even the best cleaning agent won’t perform as intended if the cleaning equipment isn’t optimized. Machine validation ensures the cleaning system—whether batch or in-line—is properly configured and consistently removing contaminants across the entire PCB.
- Impact on Reliability: Poor machine performance can lead to uneven cleaning, trapped residues under components, and inconsistent cleanliness from board to board.
- Best Practice: Validate the machine’s temperature, spray pressure, nozzle alignment, and dwell time. Routine maintenance and real-time cleanliness monitoring are essential for consistent results.
Rinsing
Once residues are dissolved, they must be removed. Rinsing eliminates both dissolved flux residues and any leftover cleaning chemistry. Failure to rinse effectively can be worse than not cleaning at all.
- Impact on Reliability: Incomplete rinsing can leave behind ionic material that attracts moisture, causes dendritic growth, or leads to electrical leakage and corrosion.
- Best Practice: Use deionized (DI) water, ensure adequate flow and duration, and monitor rinse water quality. Pay special attention to components with tight standoff gaps or shadowed areas.
Common Reliability Issues from Poor PCB Cleaning
Improper or insufficient cleaning can result in a range of reliability problems:
- Electrical Leakage and Dendritic Growth: Ionic residues attract moisture, which leads to corrosion and conductive pathways forming between conductors.
- Solder Joint Degradation: Flux trapped under or around joints can cause long-term joint degradation, especially in humid or high-voltage environments.
- Field Failures and Reduced MTBF: Contaminated boards are more likely to fail in the field, leading to costly recalls and warranty claims.
Magnalytix’s Approach to PCB Cleaning Reliability
At Magnalytix, we know that effective PCB cleaning is more than just running boards through a washer. It requires a holistic, data-driven approach—and that’s where we come in.
Tailored Cleaning Chemistry Recommendations
We help customers evaluate and select cleaning agents suited to their process materials. Whether you’re using no-clean, water-soluble, or RMA fluxes, we ensure your chemistry delivers results without compromising components.
Machine Validation and Process Optimization
We work with manufacturers to validate cleaning equipment performance using real-world board assemblies. Our team uses industry-standard test vehicles and advanced tools to simulate conditions and verify cleaning efficacy.
Advanced Cleanliness Testing
Our testing services—including Surface Insulation Resistance (SIR), Ionic Contamination (IC), and C3 testing—quantify how well you're cleaning and rinsing processes are performing. We don’t just provide numbers; we interpret the data and deliver actionable insights.
Conclusion
Effective PCB cleaning is a critical contributor to the long-term reliability of electronic assemblies. By carefully managing cleaning agent selection, machine validation, and rinsing, manufacturers can prevent costly failures and meet the demands of high-reliability applications.
At Magnalytix, we combine decades of hands-on experience with cutting-edge testing methods to help our customers achieve—and maintain—cleanliness standards that drive reliability. Whether you’re validating a new process or troubleshooting an existing one, our team is ready to support you every step of the way.
For more information on how Magnalytix can help you improve your PCB cleaning process and ensure reliability, contact us. Together, we can build assemblies that pass the test of time—with cleanliness you can count on.